The Orion project, mentioned in another post here, has video output capabilities like the Nokia N900 and other smart phones using the TI OMAP35xx series processors. These chips have dual 10 bit D/A converters for generating analog video signals, either in S-Video format (separate luminance and chrominance) or composite NTSC or PAL analog signals. Video out had been tested early on with the first version of the board, but the final production board failed FCC part 15 at the test lab recently with the issue traced to the video circuit. Even with the video output cable properly terminated in 75 ohms there were massive parasitic oscillations on the sync and blanking portion of the signals and in some instances on the entire video signal over the whole frame. Based on very limited information in the TI Technical Reference manual for the OMAP35xx processor and information from other applications, we used the feedback circuit pictured below for the composite video output:
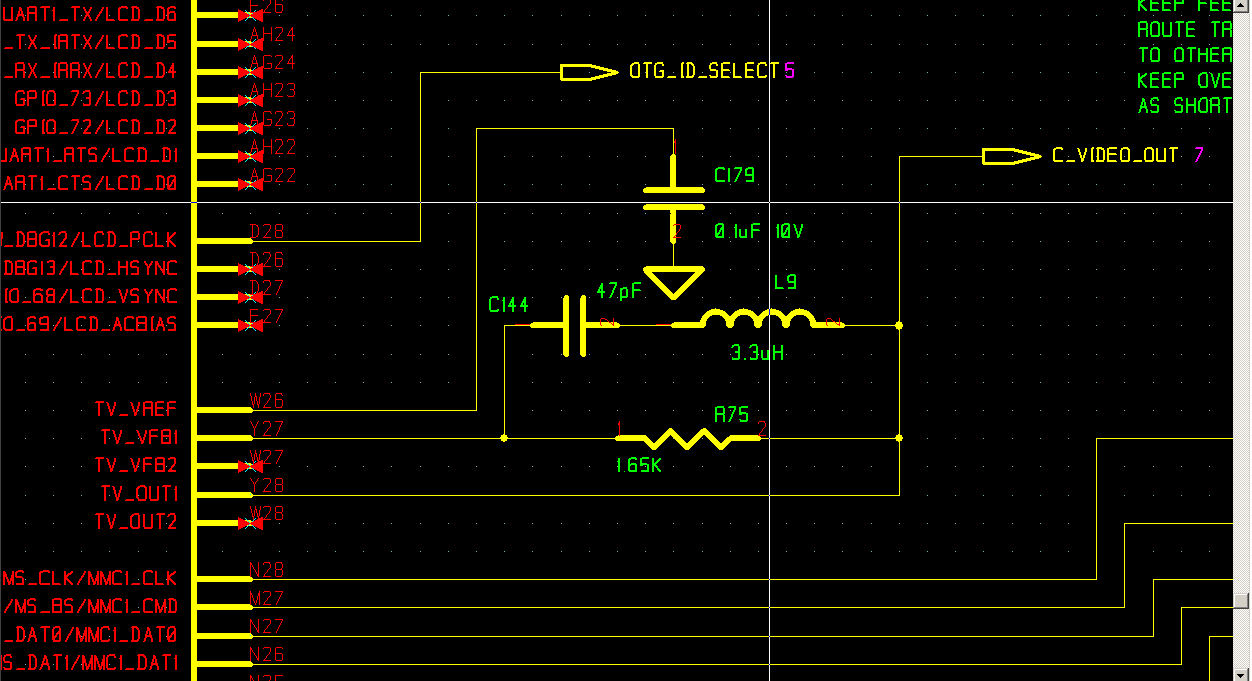
OMAP Video Feedback Circuit
Unfortunately, with the latest version of the OMAP silicon on the most recent boards, the video output, even with proper 75 ohm termination, was exhibiting nasty parasitics as shown below:
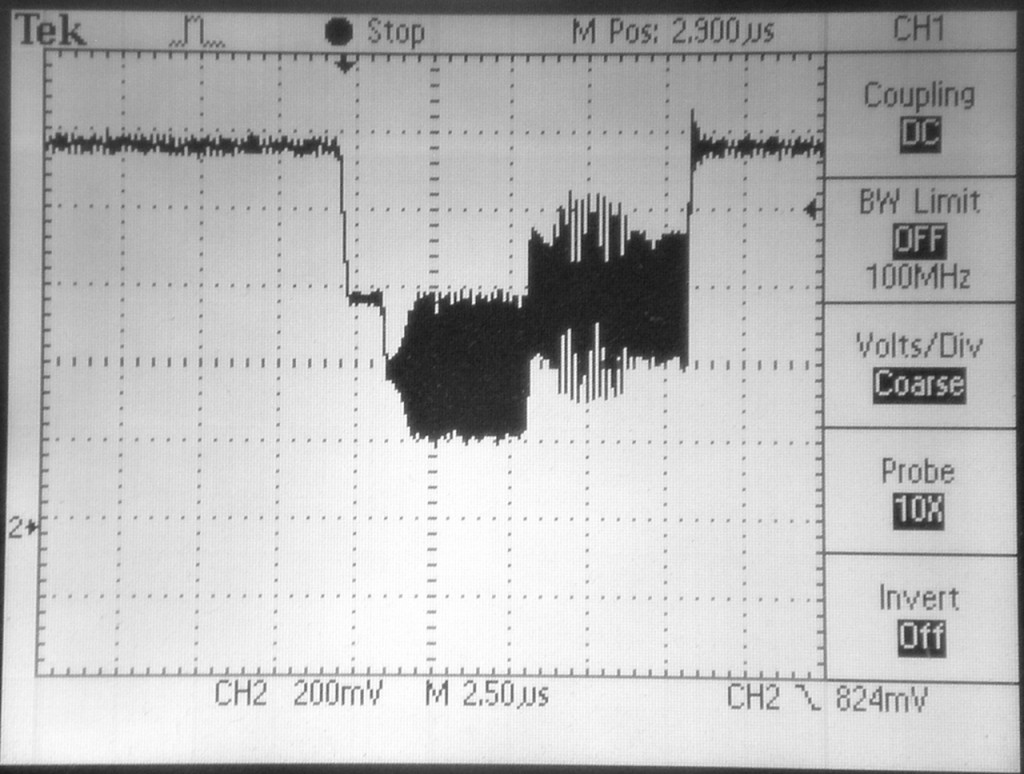
Horizontal Interval
After creating a test schematic in Linear Tech’s LT Spice IV then running some analysis on it, this gave some indication of where the trouble might be. As shown in the plot below the pole in the resonant circuit was around 12.7MHz, whereas the parasitics were between 16MHz to 19.3MHz. After manipulating the values of R75 and C144 shown in the schematic above the pole in the response of the network moved out to about 20MHz. After doing the plots and determining the component values it was time to modify the board.
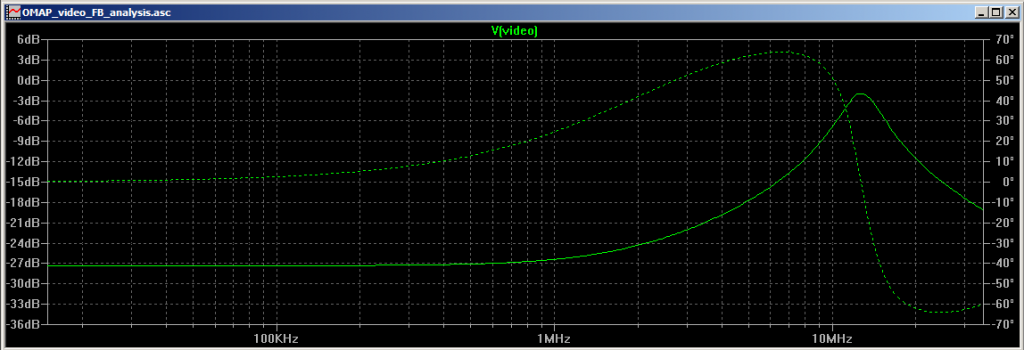
Spice Plot, Response of Feedback Network (original values)
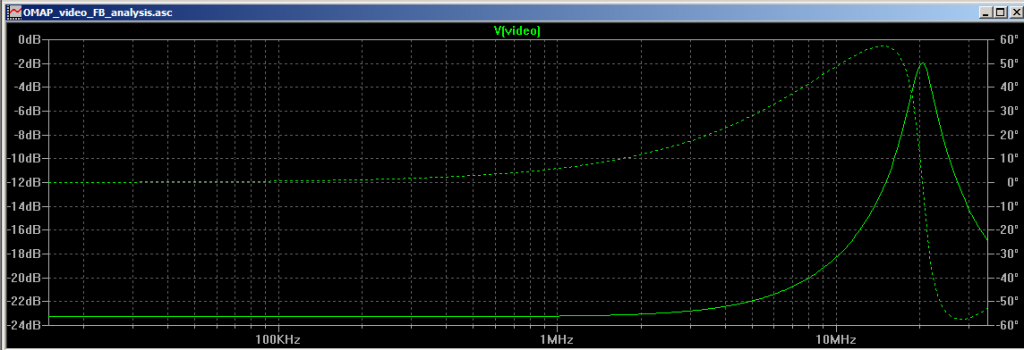
Spice Plot of Feedback Network, new values.
After modifying the board with new values for R75 (1.00K) and C144 (18pF) we measured the video again. Note that the baseline amount of feedback increased by about 4dB and the filter’s peak response narrowed somewhat. Nonetheless now we can see that the video output is stable once again:
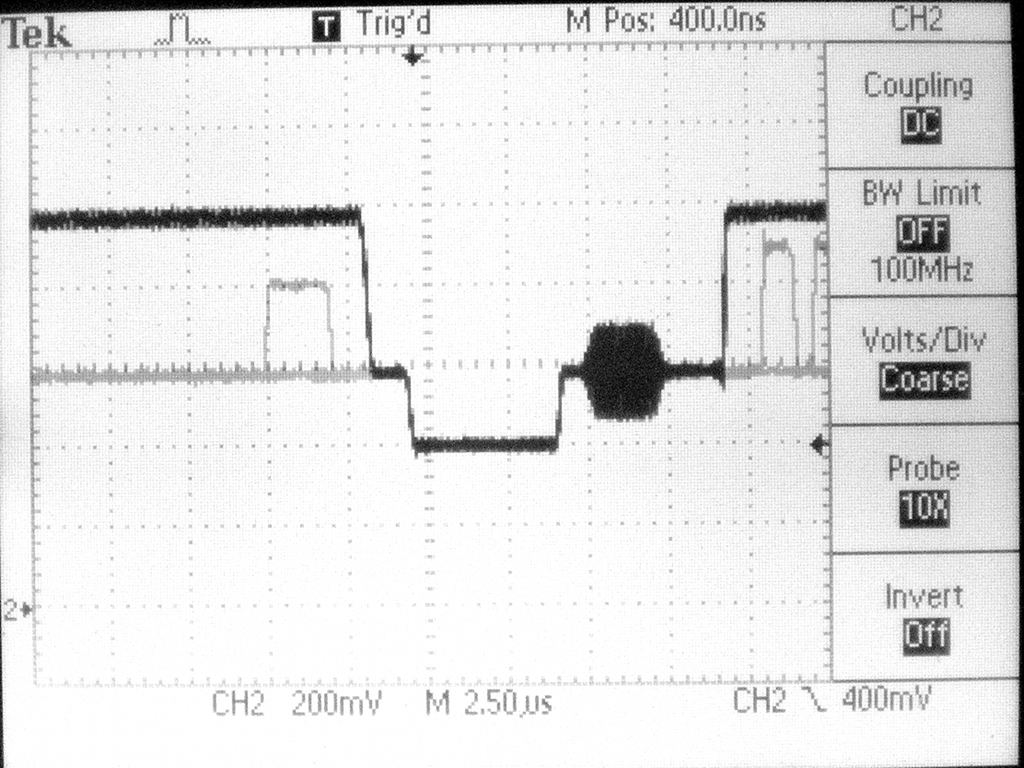
Horizontal Interval (NTSC) After Feedback Network Changes
The TI Technical Reference Manual for the OMAP processor mentions that the output amplitude of the peak to peak video signal is low, but they claim this is ok. I beg to differ. Indeed it is about 600mV to 700mV peak to peak, whereas NTSC video, sync tip to peak white, is 1.0Vpp. Some TV’s can probably work with this for sure, but my Panasonic plasma display would not lock up to it. I could see stuff parading across the screen but it always complained that there was no signal on the analog input. So beware. NTSC composite output is probably of little value anyway these days, except if you have a system like the Orion that has no other video display method. But for this product video output is not a primary use case, so the video quality (or lack thereof) isn’t a show stopping concern.